Soldadura ultrasónica
Procesos > ► Soldadura
Soldadura de plástico por ultrasonido
La soldadura ultrasónica es un proceso relativamente nuevo. La soldadura ultrasónica es una técnica industrial mediante la cual las vibraciones acústicas ultrasónicas de alta frecuencia se aplican localmente a las piezas de trabajo que se mantienen juntas bajo presión para crear una soldadura de estado sólido. Se usa comúnmente para plásticos, y especialmente para unir materiales diferentes. En la soldadura ultrasónica de plásticos, un movimiento vibratorio en la superficie de la bocina (amplitud) se transfiere a la pieza. Las vibraciones se mueven a través de la pieza y crean fricción en la interfaz entre las partes. Creando calor y luego fundiéndose. Cuando se enfría, se forma una soldadura. En la soldadura ultrasónica, no hay pernos de conexión, materiales de soldadura o adhesivos necesarios para unir los materiales. Ocasionalmente, las personas confundirán la soldadura por vibración y la soldadura ultrasónica porque ambos procesos utilizan energía vibratoria para soldar conjuntos de plástico. Sin embargo, ambos procesos son muy diferentes entre sí. Veamos las diferencias entre los dos procesos y cómo puede usarlos en su beneficio. Tanto la soldadura por vibración como la soldadura ultrasónica utilizan la vibración para crear fricción y generar calor para soldar plásticos. La soldadura ultrasónica es una técnica industrial mediante la cual las vibraciones acústicas ultrasónicas de alta frecuencia se aplican localmente a las piezas de trabajo que se mantienen juntas bajo presión para crear una soldadura de estado sólido. Se usa comúnmente para plásticos, y especialmente para unir materiales diferentes. En la soldadura ultrasónica, no hay pernos de conexión, materiales de soldadura o adhesivos necesarios para unir los materiales. Ocasionalmente, las personas confundirán la soldadura por vibración y la soldadura ultrasónica porque ambos procesos utilizan energía vibratoria para soldar conjuntos de plástico. Sin embargo, ambos procesos son muy diferentes entre sí. Tanto la soldadura por vibración como la soldadura ultrasónica utilizan la vibración para crear fricción y generar calor para soldar plásticos. La soldadura ultrasónica utiliza amplitudes mucho más pequeñas que la soldadura por vibracion. Muchas aplicaciones utilizan entre 25 y 125 micrones o 0.025-0.125 mm. Al igual que en la soldadura por vibración, cuanto menor es la amplitud, mayor es la frecuencia.
Los ultrasonidos se utilizan en los sectores más variados, como plásticos, textiles, automoción, envasado, termoformado, etc. Las ventajas de la tecnología avanzada como la soldadura ultrasónica son numerosas:
- Ciclos de soldadura muy cortos (desde unas pocas décimas de segundos por segundo)
- Absoluta constancia de resultados
- Consumo de energía muy bajo y relativo solo a la fase de soldadura
- Sin material de relleno
- Las piezas son estéticamente perfectas, muy resistentes e inmediatamente listas para usarlas
Para obtener más información sobre nuestras máquinas de soldadura contáctenos en el siguiente correo electrónico: tech@mexpolimeros.com
Gama de producto
- Potencia de 400 a 2500 W
- Voltaje de la fuente de alimentación: 115V-240V
- Filtro de red antirruido
- Accionamiento electroneumático, regulación energética
- Válvula de solenoide de baja tensión controlada por servo
- Regulador de presión de alta precisión
- Filtro de descarga de condensado semiautomático / automático
- Presostato con rango de presión ajustable
- Celda de carga controlada electrónicamente
- Ajuste del tiempo de disparo, de soldadura y de enfriamiento
- Ajuste de amplitud de 30-100% (opcional)
- Ajuste de altura mediante motor sin escobillas (opcional)
- Función de control de frecuencia, de energía y contador de piezas
- Circuito de protección de sobrecarga y protección de temperatura
- Ventilador
Soldadura por ultrasonidos
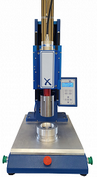
Para unir piezas complejas de termoplásticos moldeados por inyección, la soldadura por ultrasonidos es la más indicada ya que puede ser personalizada fácilmente para adaptarse a las especificaciones exactas de las piezas a soldar. La soldadura por ultrasonidos de termoplásticos produce la fusión local del plástico a causa de la absorción de la energía vibratoria y se puede emplear para plásticos duros, blandos y semicristalinos. Este proceso es una buena alternativa automatizada a la cola, tornillos o diseños de encaje a presión.Las principales ventajas del soldado por ultrasonidos son un tiempo de secado muy rápido, la no necesidad que las piezas permanezcan en una guía durante largos períodos de tiempo esperando que las justas sequen o se curen y la posibilidad de automatizar fácilmente la soldadura, realizando uniones limpias y precisas.La creciente demanda de componentes plásticos y electrónicos en diversos procesos industriales ha motivado que este tipo de soldadura haya alcanzado cotas de desarrollo tecnológico muy avanzadas y que sea una de las más utilizadas. En este sentido se puede hablar ya, por ejemplo, de la soldadura por ultrasonidos robotizada o de la soldadura por ultrasonidos multipunto. En el primer caso se trataría de una tecnología para soldar materiales plásticos por medio de un sonotrodo ubicado en el extremo del robot, equipado con un sistema de cambio rápido de sonotrodo que convierte el sistema en multifunción; y en el segundo caso estaríamos hablando de equipos de soldadura equipados simultáneamente con varios generadores de ultrasonidos capaces de soldar al mismo tiempo varios puntos.
Descripción del procedimiento
La técnica de soldadura por ultrasonidos para plástico se incluye en el procedimiento de soldadura por fusión. El procedimiento se basa en la transformación de la energía de fricción y vibración en calor. Las vibraciones de alta frecuencia generadas por el sistema ultrasónico se transmiten por presión a través de la herramienta de soldadura, llamada sonotrodo, a las piezas que se desean unir, lo que produce una vibración relativa en la zona de unión. La microfusión derivada del calor de fricción forma una barrera contra las vibraciones de modo que la energía vibratoria se absorbe y se transforma en calor, lo que hace que el contorno de soldadura se funda en décimas de segundos y, con ello, se produzca una unión a nivel molecular. Por lo general, las piezas de plástico que se vayan a soldar deben presentar un contorno de soldadura acorde con el tipo de material y con los requisitos establecidos en cuanto al cordón de la junta.
Método vertical
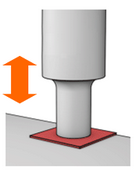
Método longitudinal
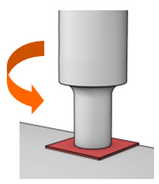
Adecuado para
La soldadura de plástico por ultrasonidos se puede utilizar con prácticamente todos los termoplásticos. A la hora de configurar juntas de piezas de trabajo a partir de plásticos semicristalinos, es necesario tener en cuenta que el comportamiento de soldadura de este tipo de plásticos se diferencia fundamentalmente del de los plásticos amorfos.
Ámbitos de aplicación
La soldadura de plástico por ultrasonidos se puede utilizar con prácticamente todos los termoplásticos. A la hora de configurar juntas de piezas de trabajo a partir de plásticos semicristalinos, es necesario tener en cuenta que el comportamiento de soldadura de este tipo de plásticos se diferencia fundamentalmente del de los plásticos amorfos. Las estructuras soldadas mediante el procedimiento longitudinal y el torsional son muy distintas entre sí. En cierta medida, también es posible unir distintos tipos de termoplásticos (plásticos amorfos). El Duroplast no se puede soldar con ultrasonidos. Actualmente, la tecnología de unión por ultrasonidos se utiliza en todos los ramos de la industria en los que se procesan plásticos.
Generador
El generador convierte la energía eléctrica de la red monofásica a la frecuencia y voltaje correctos para que el transductor se convierta en vibraciones mecánicas. La unidad de microprocesador controla el ciclo de soldadura y retroalimenta la información clave de soldadura al usuario, a través de la interfaz de usuario. La interfaz de usuario también permite al operador ingresar los parámetros de soldadura requeridos.
Prensa de máquina
El soporte de la máquina está diseñado para sostener el sistema de soldadura o la pila y aplicar la fuerza necesaria para soldar. Consiste en una placa base, para sujetar la plantilla de herramientas, y un cilindro neumático para aplicar la fuerza. La máquina tiene un manómetro y un regulador para el ajuste de la fuerza de soldadura. Cabe señalar que una determinada presión manométrica establecida en una pieza del equipo de soldadura ultrasónica no proporcionará necesariamente la misma fuerza de soldadura que otra máquina configurada con la misma presión manométrica. La fuerza de soldadura debe calibrarse usando una celda de carga para que se pueda hacer una comparación directa de las fuerzas de soldadura de una máquina a otra. También hay una válvula de control de flujo para permitir el ajuste de la velocidad a la que el cabezal de soldadura se acerca al componente que se está soldando. Algunos fabricantes de equipos han introducido un sistema de aplicación de fuerza electromagnética en lugar del cilindro neumático tradicional. Esto proporciona un mejor control de la velocidad de aproximación y puede ser beneficioso al soldar componentes pequeños o delicados.
Pila de soldadura
Esta es la parte de la máquina que proporciona las vibraciones mecánicas ultrasónicas. Generalmente es una unidad de tres partes que consta de un transductor, un amplificador y una bocina de soldadura, montados en la prensa de soldadura en el punto central de la sección del amplificador. La pila es un resonador afinado, más bien como un diapasón de instrumento musical. Para que funcione, la frecuencia de resonancia de la pila de soldadura sintonizada debe coincidir estrechamente con la frecuencia de la señal eléctrica del generador (dentro de los 30 Hz).
Transductor
El transductor, también conocido como convertidor, convierte la energía eléctrica del generador en las vibraciones mecánicas utilizadas para el proceso de soldadura. Consiste en una serie de discos cerámicos piezoeléctricos intercalados entre dos bloques de metal, generalmente de titanio. Entre cada uno de los discos hay una placa de metal delgada, que forma el electrodo. A medida que la señal eléctrica sinusoidal se alimenta al transductor a través de los electrodos, los discos se expanden y contraen, produciendo un movimiento axial de pico a pico de 15 a 20 µm. Los transductores son dispositivos delicados y deben manipularse con cuidado. Una vez que los elementos se rompen, el transductor no funcionará. Aumentador de presión La sección de refuerzo de la pila de soldadura tiene dos propósitos, principalmente para amplificar las vibraciones mecánicas producidas en la punta del transductor y transferirlas al cuerno de soldadura. Su propósito secundario es proporcionar una ubicación para montar la pila en la prensa de soldadura. El amplificador se expande y contrae cuando el transductor aplica la energía ultrasónica. El amplificador, al igual que otros elementos de la pila de soldadura, es un dispositivo sintonizado, por lo que debe resonar a una frecuencia específica para transferir la energía ultrasónica del transductor al cuerno de soldadura. Para que funcione con éxito, el amplificador debe tener la mitad de una longitud de onda de ultrasonido en el material con el que está fabricado, o múltiplos de esta longitud. Normalmente, tiene media longitud de onda.
Cuerno de soldadura
El cuerno de soldadura es el elemento de la pila de soldadura que suministra energía al componente que se está soldando. El diseño de la bocina de soldadura es fundamental para una soldadura exitosa. Se recomienda encarecidamente que la fabricación de bocinas de soldadura solo la realicen empresas especializadas en soldadura por ultrasonidos.La bocina de soldadura, al igual que el elemento de refuerzo, es un dispositivo sintonizado que, en la mayoría de las aplicaciones, también proporciona ganancia mecánica. Normalmente se fabrica en aluminio o titanio. Los cuernos de soldadura de aluminio tienden a usarse para aplicaciones de bajo volumen, ya que el desgaste puede ser un problema particular con este material. Algunas bocinas de soldadura tienen puntas especialmente endurecidas para reducir el desgaste durante la soldadura. Al igual que con el elemento de refuerzo, la longitud del cuerno de soldadura debe ser la mitad de la longitud de onda del ultrasonido en el material del que está fabricado, o múltiplos de esta longitud. Esto asegura que haya suficiente amplitud en el extremo del cuerno de soldadura para efectuar la soldadura. La amplitud es típicamente entre 30 y 120 µm. La forma del cuerno de soldadura es importante ya que la tensión, causada por la expansión y contracción axial del cuerno, podría provocar grietas en aplicaciones de gran amplitud. En algunas aplicaciones, el cuerno de soldadura se fabrica con ranuras en la dirección axial. Esto es para asegurar que la amplitud máxima de vibración esté en la dirección longitudinal. La punta del cuerno de soldadura entrega la energía ultrasónica al componente que se está soldando. La punta debe diseñarse específicamente para que coincida con el componente. Esto asegurará que se logre la máxima transferencia de energía entre la bocina y el componente. Por lo general, la punta del cuerno se perfila para que coincida con los contornos del componente.
Herramientas de apoyo
Finalmente, la base de la máquina prensa soporta el utillaje que soporta los componentes durante la operación de soldadura. Las herramientas de soporte están diseñadas para evitar el movimiento del componente inferior mientras se aplica el ultrasonido. A menudo se mecaniza para que coincida íntimamente con los contornos de la superficie del componente.
Ventajas de la soldadura por vibración
- Tiempos de soldadura rápidos (20 segundos parte a parte)
- Potencia eficiente (máquina verde)
- Recurso reutilizable (12 a 16 años de uso)
- Herramientas de cambio rápido (puede ejecutar varias partes)
- Sin marcado de las superficies
- Precisión de parte a parte dimensional
- Soldaduras fuertes
- Sellos herméticos
Planos de soldadura 2D alcanzables
Hay tres tipos de soldadura ultrasónica dependiendo de las aplicaciones que se le darán. Lo que varía en estos sistemas es la forma del sonotrodo que permitirá soldaduras en puntos específicos, continuas o circulares:
- Soldadura de punto (Spot Welding)
- Soldadura de costura (Seam Welding)
- Soldadura en torsión (Torsion Welding)
Plásticos aptos para soldadura ultrasónica:
PS, ABS, acrílico, ABS, SAN, PMMA, mezclas de policarbonato / PC, PC, ABS, mezclas, PPS, polisulfona / PSO, PVC y ASA, PPO, PC, PBT, PC, ABS, mezclas de poliéster, PET, Copolímero Nylon (Poliamida 6-3 - T), Poliamida / Nylon 6, 6/6 PBT, PP (con 30% de fibra de vidrio), PE, Poliacetal, PEI.
Factores que afectan negativamente a la soldabilidad
La higroscopicidad afecta negativamente a la soldabilidad. Si se sueldan partes húmedas, el agua atrapada dentro del material mismo se evapora y hierve cuando la temperatura alcanza el punto de ebullición. Esto crea una condición espumosa en la interfaz de la junta que dificulta la consecución de un sellado hermético y da a las piezas ensambladas un aspecto cosmético pobre. La fuerza del vínculo también se ve comprometida. La Figura 2-4 indica que la humedad resulta en ciclos de soldadura más largos. Las piezas higroscópicas deben soldarse inmediatamente después del moldeado. Si esto no es posible y las piezas deben almacenarse antes del ensamblaje, deben sellarse en bolsas de polietileno con un desecante. Es posible que las piezas almacenadas sin alguna forma de protección contra la humedad deban secarse antes de soldar.
Agentes de desmoldeo Los agentes de desmoldeo generalmente se rocían directamente sobre la superficie de la cavidad del molde y se utilizan para hacer que las piezas se expulsen de la cavidad del molde más fácilmente al reducir la fricción entre la pieza y las paredes de la cavidad. Desafortunadamente, el agente de desmoldeo en las piezas moldeadas reduce la fricción superficial en la interfaz de unión entre las piezas cuando se sueldan. Dado que el proceso de ensamblaje ultrasónico depende de la fricción de la superficie, el uso de agentes de desmoldeo puede ser perjudicial para la soldabilidad. Además, la contaminación química de la resina por el agente de liberación puede inhibir la formación de la unión deseada. Algunos agentes pueden eliminarse de las piezas con una operación de limpieza previa al montaje utilizando disolventes adecuados. Si se debe usar un agente desmoldante, se prefieren los grados que se pueden pintar / imprimir que permiten pintar y serigrafía porque interfieren menos con el ensamblaje ultrasónico y, a menudo, no requieren limpieza previa al ensamblaje. Si es posible, debe evitarse el uso de estearato de zinc, estearato de aluminio, fluorocarbonos y siliconas.
Lubricantes Los lubricantes como ceras, estearato de zinc, ácido esteárico, estearato de aluminio y ésteres grasos se agregan a resinas para mejorar las características de flujo y mejorar la procesabilidad de la resina. Dado que los lubricantes internos no se pueden eliminar y reducirán el coeficiente de fricción en las interfaces de las piezas a soldar, pueden anular todo el proceso ultrasónico.
Plastificantes Los plastificantes se utilizan para aumentar la flexibilidad y la suavidad de un material y tienen tendencia a migrar o regresar a la unión de una pieza soldada después de un período de tiempo, lo que resulta en una unión o unión debilitada. Se prefieren los plastificantes aprobados por la FDA a los plastificantes metálicos, pero se recomienda experimentar antes de la producción.
Rellenos Los rellenos como fibra de vidrio, talco, fibra de carbono y carbonato de calcio se agregan a las resinas para alterar sus propiedades físicas. Por ejemplo, se podría añadir un relleno de vidrio a una resina para mejorar su estabilidad dimensional o la resistencia del material. Los rellenos minerales comunes, como el vidrio o el talco, en realidad pueden mejorar la soldabilidad de los termoplásticos porque mejoran la capacidad de la resina para transmitir energía vibratoria, particularmente para materiales semicristalinos. Un contenido de vidrio del 10% al 20% puede mejorar sustancialmente las propiedades de transmisión de una resina. Debe reconocerse, sin embargo, que existe una relación directa entre la adición de cargas y la mejora de la soldabilidad sólo dentro de un rango cuantitativo prescrito. Cuando los niveles superan el 10% - 20%, pueden surgir otros problemas. Por ejemplo, aunque el contenido de relleno de una pieza acabada puede ser del 30% en peso, el nivel de contenido real moldeado en la junta podría ser mucho mayor. La acumulación de relleno en la interfaz de la junta (conocida como aglomeración o enriquecimiento de relleno) puede volverse tan grave que puede que no haya suficiente resina en la interfaz de la junta para formar una soldadura aceptable. Si la cantidad de relleno en la junta excede el 40%, entonces hay más material no soldable que material soldable. Esto significa que la soldabilidad se vuelve más difícil de lograr de manera consistente y la resistencia general del ensamblaje se ve afectada. Los contenidos de relleno por encima del 20% pueden causar un desgaste excesivo de la bocina y del accesorio que puede requerir herramientas especiales. Debido a la presencia de partículas en la superficie de la resina, puede ser necesario utilizar cuernos de titanio con cara de carburo o acero tratado térmicamente. También puede ser necesario un equipo ultrasónico de mayor potencia para crear suficiente calor en la junta.
Los retardadores de llama pueden afectar directamente la soldabilidad termoplástica al reducir la resistencia de la junta terminada. A menudo se requieren equipos de alta potencia, que operan a amplitudes más altas de lo normal, para que las piezas se puedan "soldar" para lograr la resistencia adecuada.
Triturado Molienda es el término que se le da al material plástico que ha sido reciclado o reprocesado y agregado a la resina original. El ensamblaje ultrasónico es uno de los pocos métodos de procesamiento que permite el reafilado de piezas, ya que no se introduce ninguna sustancia extraña en la resina. Siempre que el porcentaje de triturado no sea excesivo y el plástico no se haya degradado o contaminado, deberían surgir pocos problemas. Sin embargo, para obtener los mejores resultados, es aconsejable mantener el porcentaje de triturado lo más bajo posible.
Colorantes Los colorantes líquidos o secos, o los pigmentos, tienen muy poco efecto sobre la soldabilidad a menos que el porcentaje de colorante a resina sea excesivamente alto. Las partes blancas y negras a menudo requieren más pigmentos que otros colores y pueden causar algunos problemas. Diferentes colores de la misma pieza pueden resultar en diferentes parámetros de configuración. Se recomienda experimentar antes de la producción completa. Grado de resina El grado de resina puede tener un efecto significativo en la soldabilidad de una aplicación. El grado de la resina es importante porque diferentes grados del mismo material pueden tener temperaturas de fusión muy diferentes, lo que da como resultado soldaduras deficientes o aparente incompatibilidad. Siempre que sea posible, se deben utilizar materiales del mismo grado en el proceso de ensamblaje ultrasónico.
Productos aplicables a la soldadura ultrasónica
Esta técnica rápida y eficiente crea un sello sólido, limpio y hermético, aumentando la producción sin comprometer la calidad. Se usa para empaque, dispositivos médicos y otras aplicaciones especializadas que requieren un sello de alta calidad. Las soluciones de mesa de trabajo de alto rendimiento y completamente automatizadas crean un sello confiable sin usar insumos. Esta tecnología avanzada le ayuda a cumplir los objetivos ambientales aumentando la capacidad de reciclaje, reduciendo el material de empaque y eliminando los adhesivos y solventes químicos.
Por sector
Eléctrico, Iluminación: enchufes, enchufes, bobinas de alambre, carretes, cajas de tubos fluorescentes, interruptores de relé, cajas de fusibles, carcasas de linternas, luces de señalización, chasis de plástico.
Ordenador y oficina: barreras contra la humedad, manijas de dispositivos, botellas de tinta, bolígrafos y carcasas de máquinas de escribir, discos USB, pelotas de golf, componentes de altavoces, marco de fotos, casete, flash estéreo, carcasa de cámara, proyector, carcasa de telescopio binocular.
Suministros para el hogar: cafeteras, mangos en planchas eléctricas y bandejas separadoras de hervidores y cajas de enfriamiento, filtros para tapas de separadores, partes funcionales para procesadores de alimentos, secadores de cabello, boquillas y accesorios para aspiradoras, encendedores, filtro de café, manijas para muebles.
Transporte: retrorreflectores, luces de techo, luces traseras, espejos retrovisores para bicicletas, señales triangulares de advertencia, señales de tráfico, parasoles, espejos interiores y exteriores para vehículos, salpicaderos de automóviles, equipaje, paneles de paneles, cubiertas de bocinas, parachoques y guardabarros, cierre de cinturón de seguridad dispositivos, marco del tablero de instrumentos, aleta de aire del ventilador y volantes.
Deportes, ocio, artículos para pasatiempos, juguetes: esquís, gafas de esquí, conchas de juguete, piezas de juguete, trenes de juguete, coches de juguete, etc., tanques de agua, mango de cuchillo
Equipo médico, cosméticos: frascos, espejo de maquillaje, ejes de cepillos de dientes eléctricos, recipientes para cepillos de dientes eléctricos, cabezales y tapas de tubos, recipientes de moldeo por soplado con boquillas moldeadas por inyección, botella y tapas de yogur, riñón artificial, filtro biológico.
Material | Campo cercano | Campo lejano | Amplitud de soldadura |
Polímeros amorfos | **20 kHz (microns) | ||
Acrilonitrilo butadieno estireno (ABS) | 1 | 2 | 30-70 |
Acrilato de acrilonitrilo estireno (ASA) | 1 | 1 | 30-70 |
Copoliéster | 3 | 5 | 70-120 |
Policarbonato (PC) | 2 | 2 | 40-80 |
PC / ABS | 2 | 2 | 60-100 |
Policarbonato / Poliéster | 2 | 4 | 50-100 |
Polieterimida (PEI) | 2 | 4 | 70-100 |
Polietersulfona (PES) | 2 | 3 | 70-100 |
Metacrilato de polimetilo (acrílico, PMMA) | 2 | 3 | 40-70 |
Óxido de polifenileno (PPO) | 2 | 2 | 50-90 |
Poliestireno (PS) | 1 | 1 | 30-70 |
Polisulfona (PSU) | 2 | 3 | 70-100 |
Cloruro de polivinilo (PVC rígido) | 3 | 4 | 40-80 |
Estireno-acrilonitrilo (SAN) | 1 | 1 | 30-70 |
Polímeros semicristalinos | |||
Polímero de cristal líquido (LCP) | 3 | 4 | 70-120 |
Polioximetileno, poliacetal (POM) | 2 | 4 | 70-120 |
Poliamida (nailon, PA) | 2 | 4 | 70-120 |
Tereftalato de polibutileno (poliéster, PBT) | 3 | 4 | 70-120 |
Tereftalato de polietileno (poliéster, PET) | 3 | 4 | 80-120 |
Polieteretercetona (PEEK) | 3 | 4 | 70-120 |
Polietileno (PE) | 4 | 5 | 90-120 |
Sulfuro de polifenileno (PPS) | 3 | 4 | 80-120 |
Polipropileno (PP) | 3 | 4 | 90-120 |